Features
Types of Concrete Houses
Everything to know about concrete houses.
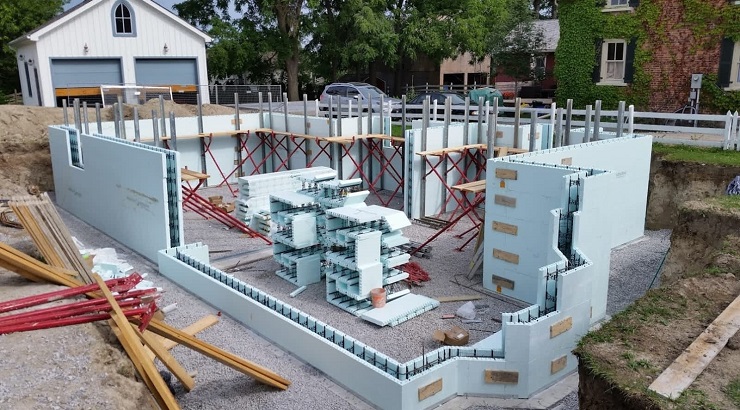
Renowned for their long-lasting, energy- conserving and cost-cutting capabilities, concrete houses are increasingly gaining popularity across the housing market.
Concrete houses, which are basically homes built with concrete as the main structural element, are so durable that they always easily outlast homes built from traditional construction materials such as wood or steel frames.
There are four types of concrete houses: concrete blocks houses, poured concrete houses, precast panels house, and insulated concrete houses, as discussed below.
1. Concrete blocks houses
Concrete block houses are easily the most affordable concrete houses. They are built by placing concrete blocks – course after the other – while ensuring the blocks are well fastened together using a suitable mortar.
Concrete blocks offer maximum defence against storms and are therefore popular in hurricane-prone areas. The materials are produced with ease and speed, and can be used with facings or coverings to create stunning home designs.
2. Poured concrete houses
Commonly referred to as cement house, poured concrete houses are made using removable wall forms that help to place insulation and reinforcing steel in aluminum, wood, or steel removable wall foams.
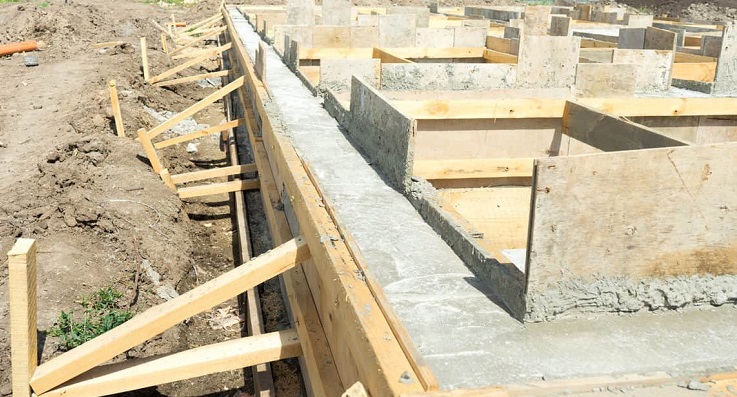
Once the concrete poured into the foams has cured, these wall foams are then removed. The concrete can be textured or patterned for aesthetic interest.
This technique allows exterior and interior walls to be poured at the same time, which shortens the construction timeline of a cement house project.
RELATED: Concrete Flooring Pros, Cons & Design Ideas
It takes about seven days for concrete to cure inside the formwork until it is solid enough for the formwork to be removed, after which the concrete continues to cure over the next couple of months until it reaches optimal strength.
3. Precast panels houses
Exterior walls of a precast panels house are created off-site at a concrete factory.
Once the foam insulation is inserted into the openings, the metal electric wiring and reinforcing are added, after which the precast panels are transported to the site for assembly.
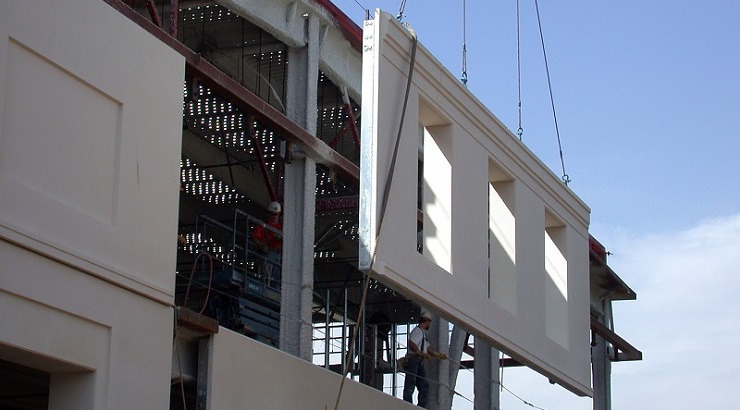
At the project site, panels are lifted by cranes and placed on the foundation and other panels, which allows for quick construction of houses.
Precast panels can be more expensive compared to other concrete houses construction options but they remain durable even in regions with hostile weather.
4. Insulated concrete houses
Easily the most durable concrete houses, insulated concrete homes are made using insulating concrete foam (IFC) – which are made of extremely dense plastic foam and filled with concrete and steel reinforcement.
Once filled with material, IFCs create a highly-insulated, airtight thermal sandwich that can withstand fire and strong winds.
The steel reinforcement used in IFCs is buried in concrete, shielding it from corrosion and rust. On the other hand, the plastic foams are treated with flame retardants to prevent them from burning in case of a fire.
This combination of materials creates an extremely durable building.
Insulated concrete houses are a great option for homes in colder climate since the technique used in their production offers maximum insulation with outside and inside layers.
Pros / benefits of concrete houses
– Concrete frame houses can withstand exposure to the elements.
– They last longer than homes built with wood or steel frame.
– A concrete framed house is moisture and insect resistant.
– It saves cash on electricity bills and insurance. According to the US Department of Energy, insulating concrete forms can cut up to 19% of energy costs.
– Concrete houses are virtually maintenance-free.
Cons / drawbacks of concrete houses
– The initial cost of putting up a concrete home is always higher than that of a home built from other construction methods.
Concrete houses cost an additional $2 to $4 per square foot compared to a home built using traditional construction materials. However, it does pay off in the long term when offsetting energy and maintenance costs.
– Concrete houses are prone to defects that lead to structural issues.
– They are susceptible to water seepage that can damage the structure over time.
